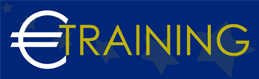

OSHA Standards
Overview:
Introduction:
This OSHA (Occupational Safety and Health Administration) Standards training program is designed to educate participants on the regulations and standards set forth by OSHA to ensure workplace safety and health. It empowers individuals with the knowledge and skills necessary to create safer work environments, reduce occupational hazards, and prevent workplace injuries and illnesses.
Program Objectives:
At the end of this program, participants will be able to:
-
Explain and apply the contents of the Occupational Safety and Health Administration 29CFR1910 (OSHA) standards.
-
Prepare an effective safety program that will also increase employee morale and productivity, and reduce overall costs.
-
Describe the training requirements of OSHA standards and identify the training topics that their organization’s employees will need.
-
Apply the record-keeping requirements of OSHA to maintain an effective workplace injury log.
-
Distinguish the difference between workers’ rights and employers’ responsibilities as defined by OSHA.
Targeted Audience:
-
Workers and employees across various industries subject to OSHA regulations.
-
Safety officers, supervisors, engineers and managers responsible for ensuring compliance with OSHA standards in the workplace.
-
Employers, business owners, and stakeholders seeking to enhance workplace safety culture and reduce incidents.
Program Outlines:
Unit 1:
Introduction to OSHA:
-
Importance of OSHA.
-
Employees’ rights and employers’ responsibilities under OSHA.
-
Contents of OSHA standards.
-
Inspections of the workplace.
Unit 2:
Fundamentals of a Safe Workplace:
-
Walking and working surfaces.
-
Hazard communication course and Safety Data Sheets (SDS).
-
Exit route, emergency action plans, fire prevention plans, and fire protection.
-
Personal Protective Equipment (PPE).
-
Fall protection.
-
Lockout/Tagout – requirements and periodic inspection.
Unit 3:
Introduction to Industrial Hygiene:
-
History of industrial hygiene.
-
Role of the safety professional.
-
Industrial hygiene fundamentals.
-
Industrial hygiene concepts and key terms.
-
Employee exposure and medical records.
Unit 4:
Industry-Specific Standards:
-
Hazardous, flammable, and combustible materials.
-
Confined space: permit required, hazards, courses, rescue.
-
Machine guarding: hazards, requirements, methods.
-
Welding, cutting, and brazing.
-
Power industrial trucks.
Unit 5:
Bloodborne Pathogens:
-
Exposure control plan.
-
Engineering and work practice controls.
-
Hepatitis B vaccination requirements.
-
What to do if an exposure occurs.
-
Training requirements.
-
Medical recordkeeping requirements.
-
Sharps injury log.