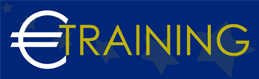

Process Plant Troubleshooting & Engineering Problem Solving
Overview:
Introduction:
Excellent Troubleshooting Skills are considered a core competency for 'Best-in-Class' modern industrial companies. If your company’s goals include minimizing downtime then this training is a must because it delivers rapid, efficient troubleshooting.
Course Objectives:
At the end of this course the participants will be able to:
- Understand how to become a 'Top Gun' Trouble-Shooter
- Develop a structured approach to Troubleshooting and Problem Solving which uses a common terminology and shared understanding
- Point the way to Continuous Improvement in the way you run your processes and make incremental efficiency gains
- Understand the difference between having a techniques manual on the bookshelf – and making it work
- Identify the "motivated" people who should be the champions of Troubleshooting and Problem Solving – and who should just follow
- Understand work practices which "allow" success in Troubleshooting and Problem Solving
Targeted Audience:
- Employees who are responsible for leading and directing people to achieve and improve productivity levels
- Those faced with the challenge of solving plant-related problems
- Production, Maintenance Engineering, and Process Engineering personnel
- Supervisors who are involved in the Operations / Maintenance function
- Planners, Coordinators, Engineers and Technologists
Course Outlines:
Unit 1: Introductory Concepts:
- The nature of problems
- A Common Terminology
- Context – Asset-based or Business Process-based
- Structured approaches – 6 Big Losses, 7 Wastes
- Techniques introduction
- Tools introduction
- A Six Level Performance Standard
- Critical Relationships
Unit 2: Tools & Techniques:
- Decision Logic
- Maturity Indexing
- Relationships Analysis
- Problem Analysis and Synthesis
- Practical Use of Tools and Techniques
- Project selection methods
- Tools & Techniques – selecting the right one
Unit 3: People Issues:
- Working practices – empowerment or impairment?
- Group dynamics
- Individual motivators
- External VS Internal Motivation
- Developing Troubleshooting and Problem-Solving skills
- Managing change
- Transition Matrix
- Fraction
Unit 4: Operator, Maintainer, Designer Interface:
- Cross-functional working
- Effect of Maintenance strategy
- Functional Contribution analysis
- Life Cycle Analysis, Design for Operation, Design for Maintenance
- Variability Analysis
- Strategies; Planning; and Protocols
- Effect of improved “Fit” between critical parameters in Operations
- Continuous Improvement
Unit 5: Review of Concepts, Tools, and Techniques:
- Action Plan
- Configuration Management
- Commercial Programs
- Application of “Standard Questions”
- The Four critical stages of Data Maturity