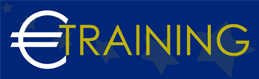

Compressor Technology
Overview:
Introduction:
This training program delivers comprehensive instruction on the design, operation, and maintenance of various types of compressors and associated systems. It equips individuals to optimize performance and minimize downtime in compressor systems across diverse industrial applications.
Program Objectives:
At the end of this program, participants will be able to:
-
Acquire skills to maximize the efficiency, reliability, and longevity of all types of compressors and bearings.
-
Apply knowledge of performance characteristics and selection criteria to size and choose dynamic and positive displacement compressors effectively.
-
Utilize advanced fault detection techniques for diagnostic testing and inspection of critical components, including common failure modes of compressors and bearings.
-
Implement strategies for selecting bearings, lubrication, compressor sealing arrangements, and conducting vibration and used oil analyses to enhance reliability and reduce costs.
-
Develop maintenance plans to minimize compressor downtime and operating costs while maximizing efficiency, reliability, and useful life.
-
Understand compressor surge and surge prevention systems to mitigate operational risks.
-
Identify causes of failures in compressors and determine design features to enhance efficiency and reliability.
-
Design various compressor systems while understanding the selection and application of sealing arrangements.
Targeted Audience:
-
Operation and Maintenance Operators.
-
Supervisors & Technicians.
-
Facility Engineers.
-
Utility Engineers.
-
Technical Professionals dealing with condition monitoring, reliability, and integrity analysis.
Program Outlines:
Unit 1:
Gas Laws, Compressor Types, and Applications:
-
Perfect and Imperfect Gases.
-
Compressor Polytropic Efficiency and Power Requirements.
-
Compressor Volumetric Flow Rate and Volumetric Efficiency.
-
Rotary and Reciprocating Compressors.
-
Dynamic Compressors (Centrifugal and Axial).
-
Compressor Performance Measurement.
-
Receivers, Compressor Control, and Compressor Unloading Systems.
-
Preventive Maintenance and Housekeeping.
Unit 2:
Positive Displacement Compressors:
-
Performance of Positive Displacement Compressors.
-
Reciprocating Compressors.
-
Reciprocating Compressors Troubleshooting and Maintenance.
-
Diaphragm Compressors.
-
Rotary Screw Compressors and Filter Separators.
-
Straight Lobe Compressors.
-
Recent Developments in Liquid/Gas Separation Technology.
Unit 3:
Dynamic Compressors:
-
Dynamic Compressor Technology.
-
Centrifugal and Axial Compressors.
-
Simplifies Equations for Determining the Performance of Dynamic Compressors.
-
Centrifugal Compressors – Components, Performance Characteristics, Balancing, Surge Prevention Systems and Testing.
-
Choking, and Anti-Choking Systems.
-
Compressor Auxiliaries, Off-Design Performance, Stall, and Surge.
Unit 4:
Dynamic Compressors Performance, Compressor Seals, and Compressor System Calculations:
-
Dynamic Compressors Performance.
-
Surge Limit, Stonewall, Prevention of Surge, Anti-Surge Control Systems.
-
Compressor Seal Systems.
-
Gas Seals, Liquid Seals, Liquid Bushing Seals, Contact Seals, Restricted Bushing Seals, Seal Liquid leakage System.
-
Dry Seals, Advanced Sealing Mechanisms, and Magnetic Bearings.
-
Compressor System Calculations.
-
Sizing of Compressor System Components, Sizing of Gas Receiver.
-
Design and Selection of Different Compressor Systems for the Oil and Gas industry, and the Power Generation Industry.
Unit 5:
Bearings, Lubrication, Vibration Analysis, and Predictive Maintenance:
-
Bearings, Types of Bearings, Thrust Bearings.
-
Lubrication, Viscosity of Lubricants, Non-Newtonian Fluids, and Greases.
-
Used Oil Analysis.
-
Vibration Analysis and Predictive Maintenance.
-
Vibration Causes, Resonant Frequency, Vibration in Predictive Maintenance, Diagnostics.
-
Intelligent (Smart Transmitters).
-
Advantages of Intelligent Instrumentation.
-
Control Valve Selection, Cavitation, and Noise.
-
Actuators, Positioners, and Accessories.
-
Diagnostic Testing.