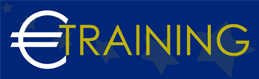

Improving Operational Performance and Productivity
Overview:
Introduction:
This training program is designed to equip participants with the knowledge and skills needed to enhance organizational efficiency and productivity. It empowers participants to drive tangible improvements in operational performance and contribute to the overall success of their organizations.
Program Objectives:
-
Identify inefficiencies and bottlenecks in operational processes and implement strategies to streamline workflows and improve productivity.
-
Utilize a variety of optimization techniques, including Six Sigma, Kaizen, and process reengineering, to enhance operational efficiency and reduce waste.
-
Establish and track key performance indicators (KPIs) to measure operational performance and analyze data to identify areas for improvement.
-
Enhance supply chain efficiency through improved inventory management, demand forecasting, supplier relationships, and technology integration.
-
Foster a culture of continuous improvement within their organization, empowering employees to contribute to ongoing operational excellence and innovation.
Targeted Audience:
-
Engineers.
-
Team Leaders.
-
Middle Managers.
-
Department Heads.
-
General Managers.
-
Project Managers.
Program Outline:
Unit 1:
Understanding Operational Efficiency:
-
Overview of operational performance and productivity concepts.
-
Identifying key performance indicators (KPIs) for operational efficiency.
-
Analyzing process flows and identifying bottlenecks.
-
Implementing lean principles to streamline operations.
-
Utilizing technology and automation to enhance efficiency.
Unit 2:
Process Optimization Techniques:
-
Applying Six Sigma methodologies to improve process efficiency and reduce defects.
-
Implementing Kaizen principles for continuous process improvement.
-
Conducting value stream mapping to identify areas for optimization.
-
Utilizing process reengineering strategies to redesign workflows for maximum efficiency.
-
Incorporating agile methodologies to adapt processes to changing demands.
Unit 3:
Performance Measurement and Analysis:
-
Establishing performance metrics aligned with organizational goals.
-
Implementing performance tracking systems to monitor progress.
-
Analyzing performance data to identify trends and areas for improvement.
-
Utilizing data visualization techniques to communicate performance insights.
-
Implementing performance reviews and feedback mechanisms for continuous improvement.
Unit 4:
Enhancing Supply Chain Efficiency:
-
Understanding the role of supply chain management in operational performance.
-
Optimizing inventory management to reduce costs and improve efficiency.
-
Implementing demand forecasting techniques to better plan production and distribution.
-
Strengthening supplier relationships and implementing vendor management strategies.
-
Utilizing technology solutions such as RFID and IoT to improve supply chain visibility and efficiency.
Unit 5:
Building a Culture of Continuous Improvement:
-
Fostering a culture of innovation and continuous improvement within the organization.
-
Empowering employees to identify and implement process improvements.
-
Providing training and development opportunities to enhance skills and knowledge.
-
Recognizing and rewarding individuals and teams for contributions to operational excellence.
-
Establishing mechanisms for sharing best practices and lessons learned across the organization.