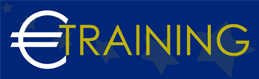

Conference on Decision Analysis for Operation and Maintenance Professionals
Overview:
Introduction:
This conference examines lean thinking and decision analysis techniques, with an emphasis on a lean approach and responsiveness to customer requirements. It provides participants with the skills needed to optimize operational and maintenance decisions.
Conference Objectives:
At the end of this conference, participants will be able to:
-
Improve productivity through the use of timely and accurate information.
-
Understand how world-class organizations solve common asset management problems.
-
Optimize the planning and scheduling of resources.
-
Conduct optimized failure analyses.
-
Develop asset management budgets that avoid unplanned equipment failures.
-
Create actionable strategies for implementing advanced decision analysis in their areas of responsibility.
Target Audience:
-
Operations Professionals.
-
Maintenance Professionals.
-
Reliability Engineers.
-
Key Operations Supervisors.
-
Internal Improvement Consultants.
Program Outline:
Unit 1:
Introduction to Decision Making in Operations and Maintenance:
-
The significance of decision-making in operational contexts.
-
Decision-making processes: how they affect outcomes.
-
Projecting outcomes for better resource allocation.
-
Decision Tree Analysis: evaluating decisions with low-probability, high-impact outcomes.
-
Monte Carlo Simulation for risk assessment and decision optimization.
Unit 2:
Implementing Multiple Criteria Decision Analysis (MCDA):
-
Definition and application of Decision Analysis.
-
Understanding why bad decisions occur and how to avoid them.
-
Limitations of traditional decision-making approaches.
-
Guidelines for effective decision analysis using multiple criteria.
Unit 3:
Analytic Hierarchy Process (AHP) and Resource Allocation:
-
Introduction to the AHP methodology.
-
Comparative matrices and consistency analysis.
-
Sensitivity analysis for decision validation.
-
Applications of AHP in maintenance strategies, resource planning, and case studies.
-
Benefit/Cost analysis for effective resource allocation.
Unit 4:
Risk Management through Failure Mode & Effect Analysis (FMEA):
-
Basics of FMEA for risk management.
-
Fault Tree analysis and how it aids in risk mitigation.
-
Risk Priority Number (RPN) and the Criticality Matrix.
-
Equipment Criticality Grading in asset management.
Unit 5:
Managing ERP and MRP Systems for Operational Efficiency:
-
Evolution of ERP and MRP systems in managing operations.
-
The difference between MRP, MRPII, and ERP.
-
Role of ERP in planning and control, including the Bill of Materials and production schedules.
-
How ERP/MRP systems improve decision-making in maintenance.
-
Scope of decisions within ERP systems for operational success.
Unit 6:
Optimum Performance Measures in Maintenance Management:
-
The importance of performance measures in continuous improvement.
-
Defining and implementing effective performance indicators.
-
Identifying desirable and undesirable features of maintenance KPIs.
-
Best and worst practices in performance measurement.
-
How performance measures drive maintenance strategies.
Unit 7:
Using Overall Equipment Effectiveness (OEE) for Best Practices:
-
Defining OEE and its role in improvement initiatives.
-
Applying lean maintenance strategies through OEE.
-
Analysis of the Six Big Losses and how to minimize them.
-
Integrating OEE into day-to-day maintenance operations.
-
Benefits of OEE in long-term asset management.
Unit 8:
House of Quality and Customer-Driven Design Solutions:
-
Basics of design evaluation using the House of Quality methodology.
-
Converting customer feedback into actionable engineering solutions.
-
Practical applications of the House of Quality in optimizing design for better performance.
-
Aligning customer needs with operational and maintenance decisions.
-
How to use the House of Quality to maintain continuous improvement.
Unit 9:
Optimizing Maintenance Decisions Using Data and CMMS:
-
Leveraging computerized maintenance management systems (CMMS) for better decision-making.
-
How CMMS can optimize maintenance scheduling and resource allocation.
-
Using data from CMMS to analyze and improve maintenance activities.
-
Benefits of integrating CMMS into asset management strategies.
-
Future trends in CMMS for maintenance optimization.
Unit 10:
Continuous Improvement in Decision-Making for Operations and Maintenance:
-
Importance of continuous improvement in operational decisions.
-
Establishing feedback loops for refining decision-making processes.
-
Tools for reviewing and enhancing decision frameworks.
-
Learning from past decisions to improve future outcomes.
-
Long-term strategies for embedding decision analysis into organizational culture.