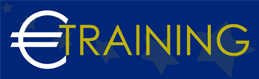

Fitness for Service API 579 1 ASME FFS1 2007
Overview:
Introduction:
This training program is an educational initiative designed to equip professionals with the knowledge and skills necessary to assess the integrity of equipment and structures in various industries. The program enables participants to effectively utilize the step-by-step 3-level approach of API 579/ASME FFS-1 2007 to evaluate inspection results, recognize potential failure modes, and implement appropriate mitigation measures.
Program Objectives:
At the end of this program, participants will be able to:
-
Determine the fitness-for-service of operating tanks, vessels, piping systems, and pipelines; and make cost-effective run-repair-replace decisions based on the principles of API recommended practice 579 "Fitness-for-Service".
-
Provides the participants with the tools necessary to recognize and assess defects in pressure vessels, storage tanks, and piping.
-
Present and apply the fundamentals rules of the ASME code to operating equipment and systems.
-
Apply API/ASME 579 "Fitness-for-Service" through examples to analyze degraded conditions and make a cost-effective repair or use-as-is decisions.
-
Apply the step-by-step 3-level approach of API/ASME 579 to evaluate inspection results and recognize potential failure modes.
-
Evaluate the structural integrity of corroded or damaged equipment, and assess their remaining life.
Targeted Audience:
-
Refinery, Petrochemical and Process Plant Mechanical and Process Engineers.
-
Technical Professionals.
-
Inspectors, Maintenance Personnel.
-
Project and Consulting Engineers.
-
Engineering and Technical Personnel involved in plant mechanical integrity and reliability.
Program Outlines:
Unit 1:
Introduction to Fitness for Service Assessment:
-
Overview of Fitness for Service (FFS) principles and objectives.
-
Understanding the regulatory framework and industry standards related to FFS assessments.
-
Identifying types of damage and degradation in equipment.
-
Introduction to the API 579/ASME FFS-1 2007 standard and its application.
-
Importance of FFS assessments in ensuring the integrity and reliability of equipment.
Unit 2:
Damage Mechanisms and Failure Modes:
-
Recognizing common damage mechanisms in equipment.
-
Understanding the behavior of materials under different service conditions.
-
Identifying failure modes associated with various damage mechanisms.
-
Case studies illustrating real-world examples of equipment failure.
-
Techniques for detecting and assessing damage in equipment.
Unit 3:
Assessment Procedures and Techniques:
-
Overview of assessment methodologies outlined in API 579/ASME FFS-1 2007.
-
Performing Level 1, Level 2, and Level 3 assessments.
-
Determining the criticality of flaws and defects in equipment.
-
Use of inspection data and engineering analysis in FFS assessments.
-
Interpretation of assessment results and decision-making processes.
Unit 4:
Repair and Remediation Strategies:
-
Selection of appropriate repair and remediation techniques based on FFS assessments.
-
Guidelines for repair welding, material upgrades, and mitigation measures.
-
Considerations for temporary repairs and emergency response situations.
-
Regulatory requirements and industry best practices for implementing repairs.
-
Case studies highlighting successful repair and remediation projects.
Unit 5:
Case Studies and Practical Applications:
-
Review of real-world case studies demonstrating FFS assessments in various industries.
-
Case study simulating FFS assessment scenarios and decision-making processes.
-
Discussion of challenges and lessons learned from past FFS projects.
-
Overview and Wrap Up.