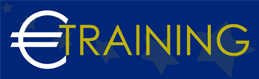

Implementing Business Process Improvement and Understanding Essential Quality and Impact Tools
Overview:
Introduction:
This training program equips participants with the necessary skills to enhance organizational processes. It empowers individuals to drive efficiency, quality, and continuous improvement within their respective organizational contexts.
Program Objectives:
At the end of this program, participants will be able to:
-
Understand the Business Process Improvement (BPI) Fundamentals.
-
Foster a Quality-Oriented Culture.
-
Enhance Problem-Solving Skills.
-
Drive Continuous Improvement Initiatives.
-
Promote Collaboration and Teamwork.
Targeted Audience:
-
Managers and Leaders.
-
Quality Assurance Professionals.
-
Process Improvement Specialists.
-
Operations Managers.
-
Project Managers.
-
Team Leaders.
Program Outlines:
Unit 1:
Introduction to Business Process Improvement (BPI):
-
Understanding the fundamentals of BPI.
-
Overview of BPI methodologies (e.g., Lean, Six Sigma).
-
Identifying opportunities for process improvement.
-
Introduction to process mapping and analysis techniques.
Unit 2:
Quality Management Fundamentals:
-
Principles of quality management.
-
Introduction to ISO standards and certification.
-
Tools and techniques for quality assurance.
-
Building a culture of quality within organizations.
Unit 3:
Essential Quality Tools:
-
Overview of essential quality tools (e.g., Pareto analysis, Ishikawa diagram, control charts).
-
Practical applications of quality tools in process improvement.
-
Hands-on exercises and case studies.
-
Assessment techniques for evaluating the impact of quality tools on process performance and efficiency.
Unit 4:
Impact Tools for Process Improvement:
-
Introduction to impact tools (e.g., Root Cause Analysis, FMEA).
-
Understanding the role of impact tools in problem-solving.
-
Application of impact tools in real-world scenarios.
-
Learning how to utilize impact tools to systematically identify and address underlying issues affecting process performance.
Unit 5:
Implementing Business Process Improvement:
-
Developing a BPI roadmap.
-
Change management strategies for successful implementation.
-
Monitoring and sustaining process improvements.
-
Closing remarks and action planning.