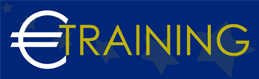

Business Process Improvement with Quality Tools
Overview:
Introduction:
This program is a comprehensive training initiative designed to equip participants with the knowledge and skills necessary to enhance organizational efficiency and effectiveness. Through a combination of theoretical concepts and practical applications, this program focuses on identifying, analyzing, and optimizing key business processes using quality tools and methodologies.
Program Objectives:
At the end of this program, the participants will be able to:
-
Identify inefficiencies and opportunities for improvement within business processes.
-
Utilize a variety of quality tools and methodologies to analyze and optimize processes effectively.
-
Implement sustainable solutions to enhance organizational efficiency and effectiveness.
-
Monitor and measure process performance to ensure continuous improvement over time.
-
Lead and facilitate process improvement initiatives within their organizations.
-
Foster a culture of continuous improvement and innovation to drive organizational success.
Targeted Audience:
-
Professionals involved in process management and optimization.
-
Quality assurance and quality control personnel.
-
Operations managers and supervisors.
-
Project managers seeking to improve project efficiency.
-
Individuals responsible for driving organizational improvement initiatives.
Program Outlines:
Unit 1:
Understanding Business Processes:
-
Identifying key business processes.
-
Analyzing process flows and dependencies.
-
Mapping current processes.
-
Identifying areas for improvement.
-
Understanding process variability.
-
Recognizing the importance of process documentation.
Unit 2:
Introduction to Quality Tools:
-
Overview of essential quality tools.
-
Understanding the purpose and application of quality tools.
-
Implementing basic quality tools such as Pareto charts and histograms.
-
Using cause-and-effect diagrams for root cause analysis.
-
Applying process flowcharts and control charts.
-
Introduction to statistical analysis for quality improvement.
Unit 3:
Process Analysis and Measurement:
-
Conducting process analysis to identify inefficiencies.
-
Measuring process performance using key metrics and indicators.
-
Analyzing process data to identify trends and patterns.
-
Using quality tools to measure process capability and variation.
-
Implementing data-driven decision-making processes.
-
Establishing benchmarks for process improvement.
Unit 4:
Implementing Process Improvement Strategies:
-
Developing and prioritizing process improvement initiatives.
-
Applying lean principles to streamline processes.
-
Implementing Six Sigma methodologies for process optimization.
-
Engaging stakeholders in process improvement efforts.
-
Implementing change management strategies for process improvement.
-
Monitoring and evaluating the effectiveness of process improvement initiatives.
Unit 5:
Sustaining Process Improvement:
-
Establishing a culture of continuous improvement.
-
Implementing process controls and monitoring mechanisms.
-
Providing ongoing training and development for process improvement teams.
-
Leveraging technology to support continuous improvement efforts.
-
Conducting regular reviews and audits of process performance.
-
Celebrating successes and recognizing contributions to process improvement initiatives.