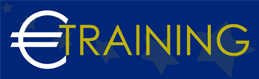

Instruments Maintenance and Control
Overview:
Introduction:
This training program provides participants with comprehensive knowledge and skills to maintain and control industrial instruments effectively. It empowers them to optimize instrumentation for better operational efficiency.
Program Objectives:
By the end of this program, participants will be able to:
-
Understand the fundamentals of industrial instrumentation.
-
Gain proficiency in preventive and corrective maintenance techniques.
-
Learn calibration and testing procedures for instruments.
-
Develop skills in troubleshooting and fault diagnosis.
- Implement best practices for instrumentation control and optimization.
Target Audience:
-
Instrumentation engineers and technicians.
-
Maintenance and reliability engineers.
-
Process control engineers.
-
Plant operators and supervisors.
-
Professionals seeking to enhance their skills in instrumentation maintenance and control.
Program Outline:
Unit 1:
Fundamentals of Industrial Instrumentation:
-
Introduction to Instrumentation Systems.
-
Types of Instruments and Their Applications.
-
Principles of Measurement and Control.
-
Instrumentation Standards and Regulations.
-
Key Components and Their Functions.
Unit 2:
Instrumentation Calibration:
-
Importance of Calibration in Instrumentation.
-
Calibration Procedures and Standards.
-
Tools and Equipment for Calibration.
-
Documenting Calibration Results.
-
Case Studies on Calibration Best Practices.
Unit 3:
Preventive Maintenance of Instruments:
-
Routine Inspection and Maintenance Procedures.
-
Cleaning and Lubrication Techniques.
-
Preventive Maintenance Schedules.
-
Maintaining Instrumentation Records.
-
Best Practices for Preventive Maintenance.
Unit 4:
Corrective Maintenance and Repair:
-
Identifying and Diagnosing Instrument Failures.
-
Corrective Maintenance Procedures.
-
Replacing and Repairing Instrument Components.
-
Testing and Validation After Repair.
-
Case Studies on Corrective Maintenance.
Unit 5:
Instrumentation Control Systems:
-
Overview of Control Systems and Automation.
-
Programmable Logic Controllers (PLCs).
-
Distributed Control Systems (DCS).
-
Supervisory Control and Data Acquisition (SCADA).
-
Integrating Instruments with Control Systems.
Unit 6:
Troubleshooting and Fault Diagnosis:
-
Common Instrumentation Issues and Causes.
-
Troubleshooting Techniques and Tools.
-
Root Cause Analysis.
-
Developing Troubleshooting Guides.
-
Examples and Case Studies.
Unit 7:
Advanced Instrumentation Techniques:
-
Digital and Smart Instruments.
-
Wireless Instrumentation.
-
Advanced Sensor Technologies.
-
Instrumentation in Hazardous Areas.
-
Emerging Trends in Instrumentation.
Unit 8:
Process Control and Optimization:
-
Principles of Process Control.
-
Control Strategies and Tuning.
-
Optimizing Instrumentation for Process Efficiency.
-
Performance Monitoring and Improvement.
-
Implementing Advanced Process Control (APC).
Unit 9:
Safety and Compliance in Instrumentation:
-
Safety Standards and Regulations.
-
Hazardous Area Classification and Safety Practices.
-
Ensuring Compliance with Industry Standards.
-
Instrumentation Safety Systems.
-
Case Studies on Safety and Compliance.
Unit 10:
Best Practices and Continuous Improvement:
-
Best Practices in Instrumentation Maintenance and Control.
-
Implementing Continuous Improvement Programs.
-
Training and Development for Instrumentation Staff.
-
Benchmarking and Performance Metrics.
-
Future Trends and Innovations in Instrumentation.