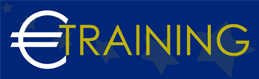

Risk Based Strategies For Inspection and Maintenance
Overview:
Introduction:
This training program is designed to provide participants with essential skills and knowledge to develop and implement risk-based approaches in inspection and maintenance activities. It empowers them to make informed decisions that mitigate risks and extend the lifespan of equipment and infrastructure.
Program Objectives:
By the end of this program, participants will be able to:
-
Understand the principles of risk-based inspection and maintenance.
-
Learn how to identify and assess risks in industrial environments.
-
Develop strategies for prioritizing inspection and maintenance activities.
-
Gain proficiency in using risk assessment tools and techniques.
-
Implement best practices for optimizing maintenance and ensuring safety.
Target Audience:
-
Maintenance engineers and technicians.
-
Inspection and quality assurance professionals.
-
Plant managers and operations personnel.
-
Risk management professionals.
-
Engineers involved in asset management and reliability.
Program Outline:
Unit 1:
Principles of Risk-Based Inspection and Maintenance:
-
Introduction to Risk-Based Approaches.
-
Benefits of Risk-Based Strategies.
-
Key Components of Risk Management.
-
Framework for Risk-Based Inspection and Maintenance.
-
Regulatory and Industry Standards.
Unit 2:
Risk Identification and Assessment:
-
Techniques for Identifying Risks.
-
Qualitative and Quantitative Risk Assessment Methods.
-
Failure Modes and Effects Analysis (FMEA).
-
Risk Matrix and Risk Prioritization.
-
Tools for Risk Assessment.
Unit 3:
Prioritizing Inspection and Maintenance Activities:
-
Criteria for Prioritizing Inspections.
-
Developing Risk-Based Inspection Plans.
-
Scheduling and Planning Maintenance Activities.
-
Balancing Preventive and Predictive Maintenance.
-
Case Studies on Effective Prioritization.
Unit 4:
Implementing Risk-Based Strategies:
-
Integrating Risk Management into Inspection Processes.
-
Developing Risk Mitigation Plans.
-
Training and Skill Development for Implementation.
-
Monitoring and Reviewing Risk-Based Programs.
-
Real-World Examples and Best Practices.
Unit 5:
Optimization and Continuous Improvement:
-
Analyzing Inspection and Maintenance Data.
-
Performance Metrics and Key Performance Indicators (KPIs).
-
Continuous Improvement in Risk-Based Programs.
-
Leveraging Technology and Software Solutions.
-
Future Trends in Risk-Based Inspection and Maintenance.