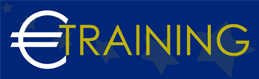

ASQ Approved Six Sigma Yellow Belt
Overview:
Introduction:
This program is designed to prepare participants for the certification exam only.
The ASQ Approved Six Sigma Yellow Belt Training Program offers foundational training on Six Sigma principles and methodologies. It empowers participants to contribute effectively to organizational goals by applying Six Sigma concepts to address process challenges and drive continuous improvement.
Program Objectives:
At the end of this program, participants will be able to:
-
Understand the fundamental principles and concepts of Six Sigma methodology.
-
Support improvement projects by applying DMAIC methodology as Yellow Belt members.
-
Identify opportunities for process improvement and contribute to problem-solving efforts.
-
Utilize basic statistical tools and techniques to analyze process performance and data.
-
Assist in the implementation of process improvements and monitor their sustainability.
Targeted Audience:
-
Employees interested in learning basic Six Sigma concepts and methodologies.
-
Team members who will support Six Sigma projects as Yellow Belt members.
-
Professionals seeking to improve their problem-solving and process improvement skills.
-
Individuals aiming to contribute to organizational efficiency and effectiveness.
Program Outlines:
Unit 1:
Introduction to Six Sigma Methodology:
-
Overview of Six Sigma methodology and its application in various industries.
-
Understanding the DMAIC (Define, Measure, Analyze, Improve, Control) process.
-
Key principles and concepts of Six Sigma, including process improvement and variation reduction.
-
Importance of customer focus and data-driven decision-making in Six Sigma projects.
-
Role and responsibilities of a Six Sigma Yellow Belt in supporting improvement initiatives.
Unit 2:
Define Phase Fundamentals:
-
Understanding the Define phase of the DMAIC process.
-
Defining project goals and objectives clearly.
-
Identifying project stakeholders and their requirements.
-
Developing project charters to formalize project scope and objectives.
-
Utilizing basic tools such as SIPOC (Suppliers, Inputs, Process, Outputs, Customers) diagrams.
Unit 3:
Measure Phase Essentials:
-
Understanding the Measure phase of the DMAIC process.
-
Selecting appropriate metrics to measure process performance.
-
Conducting data collection using various methods.
-
Understanding basic statistical concepts such as mean, median, and standard deviation.
-
Conducting process mapping to identify key process steps and variables.
Unit 4:
Analyze Phase Basics:
-
Understanding the Analyze phase of the DMAIC process.
-
Identifying potential root causes of process issues or defects.
-
Utilizing basic statistical tools such as histograms and scatter plots.
-
Conducting cause-and-effect analysis using techniques like fishbone diagrams.
-
Prioritizing root causes based on their impact on process performance.
Unit 5:
Improve and Control Phase Fundamentals:
-
Understanding the Improve and Control phases of the DMAIC process.
-
Generating and evaluating potential solutions to address root causes.
-
Developing implementation plans and conducting pilot tests.
-
Establishing control plans to sustain improvements over time.
-
Monitoring process performance and implementing corrective actions as needed.
-
Preparation for the certification exam.