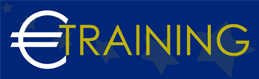

Total Quality Management: Continuous Improvement Tools
Overview:
Introduction:
Welcome to the Total Quality Management: Continuous Improvement Tools Training course! In today's competitive business environment, organizations strive for excellence in their products and services to meet customer expectations and maintain a sustainable edge. Total Quality Management (TQM) is a comprehensive approach that focuses on continuous improvement, customer satisfaction, and organizational excellence.
This 5-day training program is designed to equip participants with the essential knowledge and skills required to implement TQM principles and harness continuous improvement tools effectively. Through a combination of theoretical insights, practical exercises, and real-world examples, participants will gain the expertise needed to drive organizational excellence and achieve exceptional results.
Course Objectives:
At the end of this course the participants will be able to:
-
Learn how to identify and analyze process inefficiencies and areas for improvement.
-
Develop the ability to create and implement effective improvement plans.
-
Enhance their problem-solving and decision-making skills.
-
Gain insights into quality assurance, customer satisfaction, and employee engagement.
-
Acquire the knowledge needed to drive a culture of quality and excellence within their organization.
Targeted Audience:
-
Managers and supervisors seeking to enhance their leadership skills.
-
Quality assurance professionals.
-
Process improvement specialists.
-
Project managers and team leaders.
-
Cross-functional team members.
-
Anyone interested in understanding and implementing TQM principles and continuous improvement tools in their workplace.
Course Outlines:
Unit 1: Introduction to Total Quality Management
-
Understanding TQM principles and its relevance in today's business landscape.
-
The history and evolution of TQM.
-
Benefits and challenges of implementing TQM.
-
Building a culture of quality and excellence.
Unit 2: Continuous Improvement Tools
-
Overview of key continuous improvement tools and techniques.
-
Six Sigma methodology.
-
Lean principles and practices.
-
Kaizen and process improvement.
-
Value stream mapping.
Unit 3: Data Analysis for Improvement
-
Collecting and analyzing data for decision-making.
-
Statistical process control (SPC) techniques.
-
Root cause analysis.
-
Pareto analysis and the 80/20 rule.
-
Failure mode and effects analysis (FMEA).
Unit 4: Process Optimization and Improvement
-
Designing and optimizing processes for quality.
-
Total Productive Maintenance (TPM).
-
5S methodology for workplace organization.
-
Benchmarking and best practices.
-
Implementing improvement plans.
Unit 5: Quality Assurance and Sustainability
-
Quality management systems (ISO standards).
-
Customer satisfaction and feedback.
-
Employee engagement and empowerment.
-
Sustainability and TQM.
-
Creating a TQM roadmap for your organization.