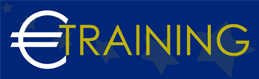

Quality and Operational Auditing
Six Sigma Yellow Belt Training Course
Overview:
Introduction:
The IASSC Certified Lean Six Sigma Yellow Belt (ICYB) is a part-time professional who is well-versed in the foundational elements of the Lean Six Sigma Methodology, leads limited improvement projects, and/or participates as a team member in more complex improvement projects led by a Certified Green Belt or Certified Black Belt. The IASSC Lean Six Sigma Yellow Belt Body of Knowledge defines a Lean Six Sigma Yellow Belt as having a full grasp of the fundamental features of the Lean Six Sigma Method, including proficiency in the subject topics covered within the Define, Measure, and Control (DMC) phases. A Yellow Belt in Lean Six Sigma knows how to implement, perform, interpret, and apply Lean Six Sigma.
Course Objectives:
At the end of this course the participants will be able to:
-
Gain a basic working knowledge of the Six Sigma DMAIC process
-
Develop an understanding of the Lean concepts and their practical application
-
Identify and reduce 8 types of waste
-
Identify process improvement opportunities
-
Develop basic problem solving & continuous improvement skills
Targeted Audience:
- Key operational Staff who have intimate knowledge of and day-to-day expertise with the company's business processes. In Lean Six Sigma Green or Black Belt projects, Yellow Belts are key contributors or team members.
- This course is also appropriate for anybody interested in gaining a broad grasp of Lean Six Sigma ideas and practices.
- Six Sigma is a lean methodology. Yellow belt training is often employed as a basic competence for all employees in world-class Lean Six Sigma organizations.
Course Outlines:
This Lean Six Sigma Yellow Belt training course covers the following areas
UNIT 1: Introduction to Lean 6 Sigma
-
What is Lean 6 Sigma?
-
Two Parts of Lean 6 Sigma
-
Focus of Lean and Lean Temple and Focus of Six Sigma and Making Customers Happy
-
How they Complement Each Other
-
Key Principles of Lean 6 Sigma and Lean 6 Sigma Belts
-
TKA Lean 6 Sigma Belt Structure and Training Roadmap
-
Role of the Yellow Belt and L6S Support Network
-
Processes and Different Ways of Looking at Process Improvement
-
What is a Process?
-
Process Concepts and Types of Process
-
Comparing Process Types, Customers, Value, and Waste
-
What are Customers? Who Wants the Outputs?
-
Tension Between the VOB and VOC
-
What Do We Mean by Value?
-
Path to Value and Dealing with Values
-
Muda (Waste) and Seven Wastes (Muda) of Lean
-
Types of Demand, Case Study Exercise and Key Metrics
UNIT 2: DMAIC Cycle
-
What is DMAIC?
-
Define
-
Common Tools for Define Phase and Gemba Tools
-
Process Stapling and Measure
-
Common Tools for Measure Phase
-
Spaghetti (Movement/Transportation) Diagrams
-
Measure Tool: Measles Charts and Analyse
-
Common Tools for Analyse Phase
-
Improve and Common Tools for Improve Phase
-
Control and Common Tools for Control Phase
UNIT 3: Yellow Belt Tools and Techniques
-
Lean Triad, 5s, Poka Yoke, SMED
-
Voice of the Customer (and CTQ’s)
-
Customer Chains and 4 Steps of VOC
-
Affinity Diagrams and Kano Diagrams
-
CTQs and Requirements
-
SIPOC
-
What is a SIPOC? An Example SIPOC
-
CSandF Web Fulfilment SIPOC
-
Creating a SIPOC and Top Tips – SIPOC
-
Value Stream Analysis and Value Stream Terminology
-
Process Maps and Aim of Value Stream Mapping
-
Swim Lanes and Typical Process Map Contents
-
Value Stream Maps and Headache Tablets: Value Stream Mapping
-
Heijunka and Heijunka in a Nutshell
-
Single Piece Flow, Pull, Kanban
-
Three-Bin System, Andon
-
Variation and SPC and Statistical Process Control (SPC)
-
Two Types of Process Variation
-
Red Bead Experiment and Standard Deviation (SD)
-
Understanding Control Charts, Defects and Process Capability, Conversion Table
-
Process Capability, Identifying Process Efficiency
-
Process Efficiency and Identifying Process Efficiency
-
Key DPMO Terms and Identifying the Root Cause(s)
-
5 Whys and Fishbone Diagram
-
Solving Problems and Problem-Solving Framework
-
Prioritisation Tools and Tools and Techniques to Generate Needed Solutions
-
Introduction to Kaizen, Kaizen in a Nutshell, and Kaizen in a Business Setting
-
Lean Teams and Introduction to Lean Team
-
Managing Progress and Demonstrating Control